引 言
近年来,随着轮胎行业的迅速发展,各轮胎企业纷纷要求以信息化为基础对传统生产线进行改造以提高综合效率和决策的可靠性,但又要避免过大的一次性投资给企业带来负担和风险,因此,在现有设备基础上对生产线进行网络信息化改造成为当务之急。炼胶是轮胎生产过程一个非常重要的环节,炼胶生产线的运行质量直接影响到轮胎的质量、成本以及效率,为了满足炼胶生产的高质量、低成本、高效率的要求,改善操作和监控环境,实现远程实时跟踪和工艺优化,提高密炼机生产管理水平,加大对炼胶生产线底层信息系统的网络化建设有着极其重要的意义。
1 问题及要求
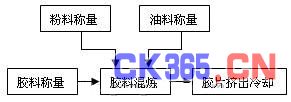
图1 炼胶生产线流程
炼胶生产线一般包括上辅机(包括胶料、粉料和油料的称量及投送系统)、胶料混炼设备(密炼机)和下辅机(胶片挤出、冷却和称量系统)三大部分(如图1所示)。传统生产线这三部分的控制系统基本相互独立,控制也相对较简单,信息“孤岛”化严重,系统难以实现工艺优化调整、生产过程在线监控和故障在线诊断预警。同时,炼胶生产环境极为恶劣:环境温度较高、大功率设备较多、粉尘及噪音严重、每一个炼胶周期较短(一般2~5分钟),并且生产线上设备分布相对较分散。为了彻底改变这种局面,需要将三部分进行有机的整合,加强生产线子系统间的信息交换、进行智能化数据融合的研究是炼胶生产线改造的重点。
针对炼胶生产线的特点及传统系统存在问题,在构建底层信息交换网络的时候应具有如下特点:(1)在干扰与被交换数据并存的环境下保证信息交换的实时性和可靠性;(2)改造过程需要保留绝大部分现有旧设备,但不同厂家不同时期的电气设备,其通信能力和通信方式参差不齐;(3)系统具备故障自诊断和预警功能,保证交换数据的可靠性和物理系统的安全性;(4)为了在线跟踪胶料质量,对胶料质量进行在线预测;(5)为了提高系统的综合性能,需要加大子系统间的信息交换能力;(6)需要考虑系统未来的可扩充性,尤其是与管理层进行信息交换。
2 系统硬件架构
2.1 系统通信方式的确定
目前,工业生产中信息交换的基本技术主要有以通用串口为基础的串行通信(如RS-232C通信、RS-422/485通信)、现场总线通信以及工业以太网。工业以太网虽然具有很大魅力,但由于小信息传输费用比较高、支持设备还不多、时间确定性和可重复性还没有根本解决等原因[1],因此目前在底层信息交换网络中以前两种为主。RS-422/485由于采用了平衡差分电路,可以实现多点通信,并且抗干扰能力强、通信距离远、通信速度较高,因此在工业数据通信中使用得比较多[2]。现场总线(FieldBus)技术是近20年来发展起来的一项工业IT基础技术,它是一种双向、串行、多节点的数字通信系统,以OSI参考模型为基础[3],连接在总线上的智能设备共享信道,进行数据和信息交换。目前,现场总线几乎成了工业数据通信与控制网络的代名词[1]。Profibus现场总线是一个多种协议并存的现场总线技术,不同协议的数据在系统内透明传输[4],是众多现场总线中能够真正实现制造业自动化、过程自动化、楼宇自动化、电力自动化的一个综合解决方案,支持的设备越来越多,具有很好的扩展能力。
在炼胶生产线基于网络化的控制系统改造中,我们选择了Profibus-DP作为底层控制网络的主体骨架,同时根据通信数据量、成本等多方面综合考虑,部分设备采用了基于RS-485的串行通信方式。
2.2 系统硬件架构
炼胶生产线需要处理信号主要包括:数字输入信号(如设备状态信号、手动控制信号等)、数字输出信号(如设备运行的开关控制信号等)、模拟输入信号(如密炼机胶料温度、系统液压压力、上顶栓压力、粉料重量、油料重量、胶料重量、电机转速、主电机功率等信号)、模拟输出信号(如上顶栓压力、电机转速等)。在生产现场一般需要的仪表有:多个重量显示仪表、多个温度显示仪表、压力显示仪表、功率显示仪表、电流表等。这些仪表多数具有一定的数字通信功能,所具有的通信方式如:RS-422/485、Profibus-DP等。
在炼胶生产线的底层控制系统设计上以Siemens S7-300为主要控制器,以工控计算机(IPC)作为监控站,并通过以太网与管理层相联。现场控制层以Profibus-DP为纽带连接现场主要智能仪表和智能设备,少部分设备由于通信功能的限制或基于改造成本等综合考虑采用RS-485串行通信,加强现场各工位人员对生产信息的直观了解和交互功能。主站PLC负责与上级监控级IPC进行信息交换,同时通过Profibus与其它智能设备(包括另外两台PLC)通信,各S7-300控制器具有相对独立性,分别处理相应子系统的数字信号和模拟信号。同时,由于炼胶过程的复杂性,目前还难以实现无人自动化,而生产线一般分布在四个楼层,为了提高效率,减少不必要的故障,现场增加两个LED显示屏(通过RS-485通信)、一个显示器(或触摸屏),以方便不同的现场人员对生产信息的了解和交互需要,并与IPC直接通信。具体如图2所示。
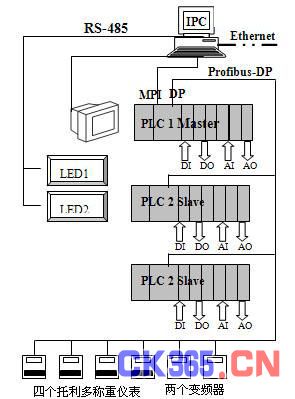
图2 炼胶生产线底层硬件架构
3 系统的软件架构
前面讨论了基于网络的底层网络系统架构,这是本文研究的基础,而系统的智能化实现是本文研究的又一主要任务,包括进行系统的故障诊断、主要质量指标的在线预测、友好的人机交互以及强大的数据库管理、工艺管理和与管理层接口等。为此,需要建立基于门尼粘度等反映混炼胶质量主要指标的预测模型以及故障诊断模型。软件系统的具体框架如图3所示。

图3 系统软件架构图
系统IPC中的整个应用软件系统自主开发,通过该软件系统实现IPC对生产线工艺配方的管理、对底层控制系统下达生产计划、在线监控、生产过程数据库的管理、数据分析、远程现场信息的显示与交互(对触摸屏)、工艺优化建模和生产质量的在线预测、在线事故诊断及预警、与管理层进行信息交换。IPC通过CP5611卡与PLC主站(Master)通过MPI接口进行通信。
整个IPC系统软件我们采用Delphi 7.0在Windows XP环境下开发,数据库采用SQL Server2000管理。
4 系统功能及特点
通过应用本系统对传统炼胶生产线进行改造,炼胶生产线控制系统的综合性能得到了提高:
(1)具有内容丰富的多点监控画面,并且能够进行远程交互(例如可以在中控室也可在现场进行生产计划的下达等);
(2)加大了必要信息的采集,子系统间信息交换和协调能力得到了大大加强,提高整个系统的运作效率和安全可靠性,有效降低了系统由于信息“孤岛化”带来的生产风险;
(3)上辅机系统(即胶料、粉料和油料称量系统)实现了手动、自动称量,并且配方修改方便、灵活;
(4)混炼系统除具备手动和普通的自动控制外,能够进行以质量为中心的智能控制,通过建立的门尼粘度在线预测模型在对质量进行预测,进而对混炼过程进行控制;
(5)通过对通信网络、设备运行状态、过程控制状况以及主要工艺数据进行实时跟踪,达到对系统的故障诊断和预警;
(6)具备了与管理层进行信息交换的能力,走出了传统系统信息孤岛的局面;
(7)同时系统具有较强的数据库管理和工艺配方编辑能力。
5 结束语
在以信息化带动传统产业的工业化进程中,对于环境恶劣、生产相对复杂的轮胎炼胶生产线进行网络化的应用研究,从软硬件系统的构建上<