钢丝绳是工程中主要的承载构件,广泛应用于煤炭、冶金、交通、运输、建筑、旅游等国民经济各主要行业和部门,其安全使用问题备受关注。长期以来 人们对钢丝绳采用人工目测和定期更换的方法来避免事故的发生,但是人工目测法可靠性差且效率低,定期更换则造成巨大浪费,据统计,更换下来的钢丝绳中 70%以上仅有很少甚至没有强度损耗[1]。
因此,研制可靠检测钢丝绳状态的无损探伤设备成为当务之急,钢丝绳无损检测技术也由此不断发展。从1906年世界出现第一台钢丝绳探伤仪到现 在,理论上探讨过的钢丝绳无损检测方法很多,包括超声波、声发射、电涡流、射线、光学及磁检测法等,其中只有磁检测法得到了实践和推广;其它方法或因检测 信号易受干扰,检测结果难以记录;或因设备费用太高,检测局限性太大,均未推广应用。经过多年的探索和实践,钢丝绳无损检测技术取得了显著的进步,对应不 同工业场合的各种钢丝绳探伤仪也相继出现。然而,因为钢丝绳本身结构和使用环境的不同,检测时钢丝绳相对传感器的径向晃动和不规则扭转,钢丝绳的拉伸程 度,损伤的深度、宽度和形态,环境温度的变化及外界的电磁干扰等,都会对检测信号产生较大影响,而且当前尚无可靠的损伤评价标准,要对损伤作出定量分析很 困难。以下对当前主要的钢丝绳无损检测方法进行分析和比较,并对实施钢丝绳定量无损检测时遇到的主要困难进行探讨。
1 主要的钢丝绳无损检测方法及其特点
钢丝绳无损检测包括两方面内容,即局部损伤检测和截面缺损测量。对这两种损伤,传统的磁检测方法有漏磁通法、主磁通法和回路磁通法,相应的检测 元件有感应线圈、霍尔元件和磁通门等,目前传感器探头有向多种磁感应元件组成的混合探头发展的趋势。20世纪90年代以后提出的检测方法包括磁致伸缩法和 声发射-超声法。探伤设备的分辨力、检测信号的特点及可靠性、辅助检测电路的结构以及后续信号处理,均由传感器探头的结构和所用检测元件决定,下面以传感 器的类型为依据分析当前主要的钢丝绳无损检测方法。
1.1 感应线圈检测法
感应线圈传感器的结构如图1所示,永磁体将钢丝绳的被测区域沿轴向磁化至饱和,钢丝绳内的磁感应强度B保持恒定,穿过钢丝绳的磁通量与钢丝绳的 横截面积成正比,因而测量钢丝绳的轴向主磁通,可以定量检测钢丝绳的截面缺损;对于局部损伤,断口处会产生漏磁场,通过测量钢丝绳表面的漏磁,可间接确定 钢丝绳的局部损伤。感应线圈检测法最大的缺点是传感器的输出和检测速度有关,检测速度不均匀时传感器输出信号产生畸变,极低速时无输出。同时,速度不均匀 会造成检测信号在时间轴上的压缩或拉伸,不利于后续信号处理,因此需将时域采样信号转换成空间域的等空间采样信号以消除速度的影响。线圈传感器要求稳定的 检测速度,尽管目前的线圈传感器加入了霍尔元件等消除速度因素的装置,并在后续信号处理中加入了速度归一化环节,但为了使检测结果可靠,仍然需要稳定的速 度。
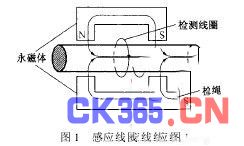
感应线圈法成本低,易实现。1906年出现的第一台钢丝绳探伤仪采用了交流励磁的感应线圈传感器,到目前,励磁方式从交流励磁和直流励磁发展为大量采用的永久励磁方式且技术日趋成熟。在R W

1.2 霍尔元件检测法
目前,钢丝绳缺陷漏磁场检测一般采用霍尔元件作为磁敏元件。霍尔元件传感器的最大优点是输出信号不受速度影响,且体积小,对小间隙空间的磁场测量有很大的优越性,因此得到广泛应用。
霍尔元件传感器的结构和线圈传感器相似,但前者的检测器件是镶嵌在传感器内壁的霍尔元件,后者是绕在钢丝绳上的感应线圈。霍尔元件用于探伤的原 理为,置于钢丝绳表面附近的霍尔元件可感应钢丝绳表面漏磁场的法向分量,并输出相应的电压信号。单纯的霍尔元件测磁灵敏度较低,大约为12 mV/mA·T,温漂大,制成的传感器电路结构复杂且不可靠。集成霍尔元件的出现解决了这个问题,美国史普拉格公司生产的集成霍尔元件UGN-3501T 线性灵敏度通常>0.7 V/ mA·T。集成霍尔元件的使用可简化钢丝绳无损检测的后续处理电路,增强检测信号的可靠性和稳定性,因此得到了推广。需注意的是,虽然霍尔元件传感器消除 了速度对信号幅度的影响,分析时依然要将时间域的信号转化到空间域,因为检测速度不恒定时,时间轴上的信号仍会随着采样速度被拉伸或压缩。
德国Stuttgart大学于1999年设计了内壁嵌有霍尔元件环形阵列的传感器探头,得到的检测信号由传统的一维信号变为可全面表征钢丝绳缺陷的三维信号,用图解法分析该信号可以清晰地描述钢丝绳轴向和周向的磁场形态[2],并作为检测钢丝绳周向分散损伤的理论根据;Zawada公司的霍尔元件探头能准确无误地检测所有严重缺陷,并确定缺陷位置和深度,检测局部损伤精度为钢丝绳横截面积的0.2%[4];南 非AATS公司的AATS Model 817,俄罗斯Intron Plus Ltd的MH&F系列均采用了霍尔元件传感器,后者检测断丝的灵敏度为横截面积的0.5%~1%,截面缺损的检测精度为1%~2%,可分辨长度在 250~500 mm以上的截面缺损;Zawa-da公司和Intron Plus Ltd研制的探伤仪还可检测不同尺寸的扁钢丝绳[2]。
我国华中科技大学金建华和康宜华等人用硅钢片模拟有缺陷的钢丝绳,用霍尔元件传感器较全面地研究了漏磁场和裂纹深度、宽度及其埋藏深度之间的定量关系,实验结果显示裂纹的实际尺寸和检测结果之间的相对误差<±4%[5];华中科技大学武新军等采用霍尔元件传感器开发了检测断丝与磨损的探伤设备,对大直径钢丝绳的断丝定量检测准确率>70%,磨损量的定量检测精度达到0.05%[6];湘潭工学院以霍尔元件为传感器设计了煤矿钢丝绳断丝在线检测仪的数据采集和信号处理系统[7]。
1.3 磁通门检测法
磁通门器件有很高的测磁灵敏度和定向性,可以静态地检测磁场强度,磁通门检测法在局部损伤检测中的效果优于线圈传感器。
磁通门检测法利用磁心材料在交变磁场的饱和激励下,由于钢丝绳缺陷漏磁场的影响而使感应输出的电压发生“非对称性”变化来检测漏磁场。目前,磁通门传感器多由单磁心单绕组磁通门组成(图2)[8]。在传感器内壁沿钢丝绳周向均匀布置这种单磁心单绕组检测回路就构成了磁通门探头(励磁方式和前两种方法相同),根据每个检测回路的输出可获取钢丝绳周向各处的磁场信息。
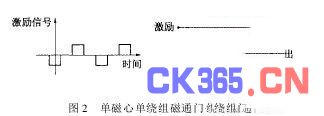
在绳长方向,每路以一个捻距间隔反向串联两个磁通门,通过差动式连接,还可省去使用霍尔元件所需的外围电路,并有效抑制检测中各种共模干扰信号,特别是钢丝绳的股波对检测的影响[9]。和线圈检测法相比,磁通门检测法的优越之处在于,对于极小的缺陷,线圈检测到的漏磁通为平均值,无法得到实际的磁感应强度;而磁通门检测法在理论上可以检测到微小缺陷磁场强度的近似值。但是磁通门法需要外加交流激励,运算比较烦琐,而且运算过程中存在系统误差。
使用磁通门传感器的例子有加拿大Rotesco的Rotescograph 2D和2C-TAG88M,这一类型的传感器对局部损伤的检测精度为截面积的0.05%,对截面缺损的检测精度为0.1%,可分辨的截面缺损的最小长度为250~530 mm[2]。上海海运学院的应力[10]等建立了基于磁通门传感器的钢丝绳损伤信号的数学模型,分析了单磁心单绕组磁通门的灵敏度和抗干扰性,通过实验分析得出,磁通门传感器能可靠地检测钢丝绳的局部损伤缺陷和截面缺损缺陷,而且获得了清晰易辨的漏磁场信号,设计了钢丝绳无损探伤的磁通门传感器。
1.4 磁致伸缩检测法
磁致伸缩法于1994年由美国西南研究所提出,此法克服了传统方法中钢丝绳必须穿过传感器的缺点,可实现钢丝绳的全过程检测。
磁致伸缩检测法的依据为铁磁材料棒在外磁场的作用下会沿磁力线方向产生伸长或缩短(磁致伸缩效应);反之,当极化了的铁磁棒发生形变时,在棒内 会引起磁场强度的变化(逆磁致伸缩效应)。磁致伸缩传感器如图3所示,信号发生器产生信号,经功率放大后,由激励线圈对钢丝绳施加瞬间的激励磁场,钢丝绳 中产生的机械波将沿构件轴向传播,如有缺陷,机械波反射回来,由于逆磁致伸缩效应,接收线圈获得反射波信号,通过信号分析获得被测构件各处的损伤状况。
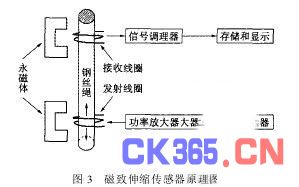
磁致伸缩法能实现大范围非接触快速检测,可有效探测被覆盖或深埋的钢铁构件,检测时间短,效率高(检测100m的钢丝绳只需要几秒钟)。存在的 问题是,目前对于磁致伸缩效应产生机械波的机理、传播特性等研究得不是很深入;磁致伸缩效应产生的信号频带很宽,要完整地采集信号各频段的信息有难度[11]。
磁致伸缩法目前还处于理论研究和传感器的研究与试验阶段,华中科技大学设计了可用于磁致伸缩无损检测传感器的大电流功率放大器;北京理工大学设 计开发了一种磁致伸缩式超声波激发/接收传感器,并通过实验验证了其可靠性,这种传感器已用于材料弹性模量的测量研究。目前还没有可用于钢丝绳无损检测的 产品出现。
1.5 声发射2超声检测法
为了实现钢丝绳状态的在线检测,国外近几年又提出一种新的检测方法,即声发射2超声检测法,它综合了声发射和超声法的优点,将超声检测引入钢丝 绳中(检测原理如图4),模拟声发射信号在钢丝绳中传播的特性,并在另一端提取信号,根据提取信号的特征计算钢丝绳缺陷。声发射2超声检测法不但能对钢丝 绳进行缺陷探测、成像和特性分析,在线评估钢丝绳的内在性能,如钢丝绳的疲劳损失、强度和硬度等,而且克服了声发射只能用于检测静态钢丝绳及捕捉断丝断开 瞬间信号的不足,可以用于动态钢丝绳的监测[11]。此方法当前尚处于理论研究阶段。
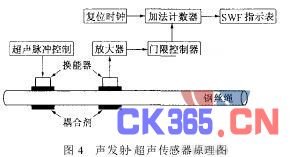
1.6 其它方法
河南洛阳涧西矿冶机电研究所的窦毓棠等采用自行研制的静态感应线圈,研制了TCK(GXT)型钢丝绳无损检测仪,这种检测方法不要求检测时钢丝 绳沿轴向励磁至饱和,但需要在检测前对钢丝绳进行直流励磁。该仪器探头灵敏度可达50 V/mT,消除了振动、晃动和股波噪声的影响,得到的钢丝绳信号曲线和检测速度无关,对单项缺陷的检测精度>95%,混合缺陷>90%,在对 直径为125 mm大桥斜拉钢缆进行检测的实践中取得了成功[12]。
综上所述,钢丝绳无损检测技术发展到今天,无论是传感器还是检测方法都取得了显著进步,与此同时,缺陷信号的处理方法也不断改进。波兰于 1978年将采集到的钢丝绳信号转换为数字信号,并依据所建立的模型反演计算,从而得到定量的损伤信息;华中科技大学在20世纪80年代通过采用等空间采 样技术和差分超门限算法实现了钢丝绳断丝数的定量检测;1995年日本学者将成像技术引入钢丝绳信号处理,实现了平行丝钢丝绳断丝的可视化检测[11];哈尔滨工业大学将小波分析和神经网络用于钢丝绳断丝信号处理,断丝定性识别成功率为100%,定量识别的成功率为88%[3,13];2003年华中科技大学采用基于事例推理的漏磁检测数据处理方法,提高了检测系统的精度和智能化程度[14]。然而,要真正实现钢丝绳损伤的定量检测仍有诸多问题亟待解决。
2 钢丝绳定量无损检测存在的重要问题
钢丝绳无损检测的目的是检测损伤并计算残余强度,最终决定钢丝绳的更换日期。而目前的研究还处于检测仪器的研究阶段,即逐渐以仪器来取代人工检 查的阶段,相对钢丝绳损伤的多态性和复杂性,当前所进行的研究还不够,与钢丝绳无损检测的最终目标距离尚远,当前需要解决的关键问题包括下面几个方面:
(1)无法测知钢丝绳的剩余载荷和钢丝绳损伤之间的定量关系。首先,钢丝绳的运行环境复杂多变,决定了损伤的多态性,而且,实验室对损伤的模拟 范围很窄,无法全面模拟实际的损伤形态;其次,影响钢丝绳性能的因素很多,且诸多因素之间的关系错综复杂,人们对钢丝绳缺陷的电磁场理论、信号特征及材料 力学分析等方面尚未形成比较成熟的理论,因此,要得到剩余载荷和损伤之间的确定关系非常困难。一些专家根据经验给出校正因数,将对损伤的估计转换成强度估 计。校正因数一般促成钢丝绳过早地报废,造成浪费,但有时也会忽略小于探伤设备分辨力(平均长度)的损伤对钢丝绳强度造成的影响[15]。
(2)检测传感器的输出和钢丝绳周围的磁场信息不是一个概念,即使是准确的磁场信息也并不能完全代表准确的损伤信息,因此要从传感器的输出定量 地确定钢丝绳损伤是无损检测面临的难题。传感器的输出不仅和钢丝绳表面磁场有关,还和检测时的提离距离、检测条件、钢丝绳状态(拉伸程度)等条件有关,所 有这些因素都使探头的建模变得异常复杂,因此寻找传感器的输出和磁场信息之间的定量关系不是简单的问题。而且,即使准确地检测到了钢丝绳表面的磁场信息, 磁场信息和实际损伤之间的关系如何确定也是个难题。
20世纪80年代以后各国无损检测专家曾尝试根据传感器输出信号定量计算钢丝绳的损伤,如美国的M J Bergander博士研究了利用检测信号估计钢丝绳缺陷的数字计算方法,并在实验的基础上推导出定量确定缺陷的计算公式;加拿大的E Kalwa博士和K Piekarski教授对钢丝绳检测装置进行了多种形式的改进,并做了大量实验,掌握了缺陷定量特征与检测信号幅度及波形之间的一些对应规律[1]。这些成果或因计算公式需要迭代求解而且很多参数的不易确定,或因实验室钢丝绳研究范围的局限性,均未能推广应用,因此这方面的研究还需继续深入。
(3)要实现截面缺损信号的可靠标定仍是难点。截面缺损标定是测量截面缺损的关键环节。传统方法通过抽除钢丝绳中若干钢丝并测量检测信号定量的 变化量实现标定,但这种人为制造的缺损与实际使用中钢丝绳的周向分散截面缺损不同,因此标定的可靠性值得推敲。此问题在涉及钢丝绳的状态时更为敏感,如对 静止的钢丝绳用以上方法标定和对运动中的钢丝绳以同样的方法标定会得到不同的结果[2]。
(4)实验室的模拟损伤不能完全代表使用现场的实际损伤。一是无法较全面地模拟实际损伤的形态,二是人为制造的损伤和实际损伤是不同的,因此从 实验中总结的规律和参数能否用于钢丝绳缺陷分析还需商榷。人为制造的损伤要尽量逼近实际情况,如制造一根断丝时,不能只是简单地锯断,应先将局部敲细,然 后再用扁铲剁开,模拟制造裂纹,同样在裂纹两边要考虑如何模拟疲劳层[15]。
(5)无损检测设备的定量分辨力对定量检测有较大影响。探伤装置的定量分辨力(或平均长度、扫描长度)表示仪器能够准确测量的截面缺损的最小长度,它是衡量探伤设备性能的重要的参数。
Herbert R Weischedel博士对不同定量分辨力的探伤仪进行实验比较,结果表明,对于定量分辨力为50 mm的LMA-TestTM探伤仪,当断丝裂口的宽度>50 mm时,截面缺损信号可以准确地反映损伤程度,断丝裂口的宽度<50 mm时则不能反映;而另一种定量分辨力为305 mm的仪器不能识别由单根断丝造成的截面缺损,只能检测到多根断丝聚集时的缺损[15~19]。现有的探伤仪分辨力最高能达到20~50 mm,要精确检测<20 mm的缺陷比较困难,因此提高检测仪器的分辨力也是实现钢丝绳定量检测不能回避的问题。
3 结论
钢丝绳无损检测的目的是确保钢丝绳的安全使用,以及在安全使用的前提下尽量减少因过早报废而产生的浪费,具有重要的经济价值。多年的研究和实践 使钢丝绳无损检测技术取得了较大发展,检测精度和检测设备的灵敏度及可靠性大大提高,探伤理论的研究也取得了卓有成效的进展,然而这一现状和钢丝绳无损检 测的最终目标距离尚远。钢丝绳缺陷的定性检测已经比较可靠,但因钢丝绳损伤的多样性、复杂性和外界干扰的影响,要定量地确定检测信号和钢丝绳损伤之间的关 系仍然很困难。
钢丝绳无损检测下一个目标是通过改进检测技术,加强钢丝绳缺陷的电磁场理论研究,拓宽试验用钢丝绳的范围,求解传感器输出和钢丝绳缺陷之间的可 靠的定量关系,上述第2部分列出的要点是实现定量检测需要解决的问题。同时,钢丝绳检测的执行人员需熟知所用设备的局限性和检测原理(包括检测漏磁通的灵 敏度、钢丝绳的结构和定量分辨力对截面缺损的影响等),以便结合经验参数对检测信号进行修正。如果能通过传感器输出得到钢丝绳定量的缺陷则有望计算钢丝绳 的剩余载荷,再结合一定的报废标准,就可预测钢丝绳的更换日期了。