诺德传动集团推出的状态监测系统能定期或永久地记录驱动系统及状态数据来优化操作的安全性和提高机器的效率。诺德还在该基础上开发了预测性维护概念,其基本原理是通过驱动电子设备中的智能PLC对模拟和数字数据(测量、信号和操作参数)进行快速、高效和全面地评估。
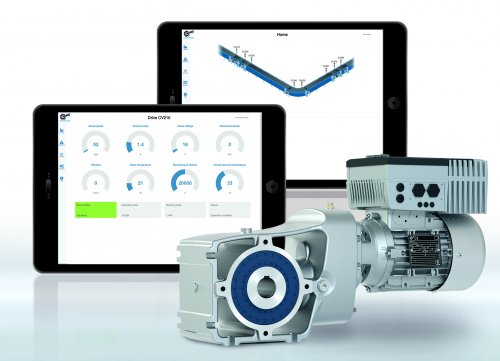
用于预测性维护的状态监测系统:诺德推出的驱动技术大大提高了机器和工厂运行的安全性和效率。图示为物流应用
预测性维护的目的是对机器和工厂进行主动维护,它能在早期阶段发现异常,旨在减少停机时间并提高整个工厂的效率。现在,状态监测维护已取代传统的周期性维护,它能尽早地发现并避免异常运行、意外停机和机器故障。预测性维护还能根据实际驱动和过程数据来规划机器和工厂的停机时间。这对于使用诺德驱动技术的工厂和机械操作员而言减少了服务和材料成本,同时提高了工厂的利用率。其另一大优势是延长了组件和机械的使用寿命,同时还可以规划维护并优化其成本。
利用驱动数据实现智能算法
诺德在驱动技术的基础上通过智能算法和虚拟传感器将信息从状态监测系统传送到预测性维护系统中。以监控油温确定换油时间为例。油温是齿轮箱中油老化的关键因素。系统将油温与齿轮箱参数和特定的运行参数结合后可以精确地推算出换油时间,无需使用物理温度传感器。诺德的变频器还集成了PLC,可通过智能算法对驱动数据进行预处理,并用作评估单元。客户可以通过所有的通用界面访问计算出的数据。
针对不同的解决方案适配PLC软件架构
诺德可根据相应的自动化任务来扩展驱动设备或对其进行调整,用户还可以直接选择需添加的驱动任务(驱动监测、驱动控制、过程控制)。在生产区域较小时,这种扩展性可为工厂判断是否需要重组提供了初步经验。诺德现有三种配置级别可供选择。在第一级中,驱动单元中的PLC仅执行驱动监测任务,并对驱动参数进行预处理,然后传至负责驱动和过程控制的高级控制系统中。在中等级别中,PLC则集成了驱动控制及运行驱动相关功能。在较高的组态级别中,变频器PLC则完全替代了较高级别的控制系统,除了能与控制单元通信外,无互联网连接的本地数据管理也能选择并应用数据。
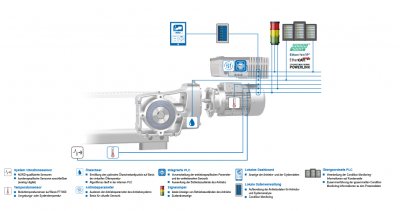
诺德进行状态监测及测性维护的基本原理是通过驱动电子设备中的智能PLC对模拟和数字数据(测量、信号和操作参数)进行快速、高效和全面地评估。